中金 | “大国重器”系列:解密特斯拉一体压铸黑科技
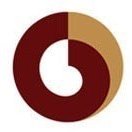
中金点睛
原标题:中金 | “大国重器”系列:解密特斯拉一体压铸黑科技 来源:中金点睛
特斯拉近期推出一体化压铸工艺并迅速应用于Model Y车身后底板的制造,其中,大型压铸机制造技术的突破成为一体化压铸工艺得以顺利应用的关键。我们认为,随着该工艺的逐步成熟,大型压铸机的渗透率也有望快速提升,建议投资者关注压铸机行业龙头及大型压铸机的领先者,同时建议关注压铸机行业优秀企业。
摘要
大型压铸机制造技术的突破有望让压铸件往大型化和集成化发展。压铸机的工作对象以铝、镁合金为主,汽车是最主要的下游。往前看,我们认为车用压铸件面临两个发展趋势:1)随着新能源汽车对轻量化要求的提升,单车用铝量有望增加,带动压铸工艺渗透率提升;2)大型压铸机制造技术的突破有望使压铸件朝着大型化和集成化发展,更多大型结构件有望用压铸来完成。
特斯拉示范性应用,有望带来传统车身制造模式的技术变革。相比传统车身制造的“冲压+焊接”工艺,一体压铸具有轻量化、零件数量及工序步骤减少、人员及土地节约等优势。特斯拉已将该工艺用于Model Y后底板的生产,将零件从70个减少到1-2个,后续有望继续用于其他车型,以及前、中底板等部件。我们认为,特斯拉的示范性应用有望带来其他新能源车厂乃至传统车厂的效仿,进而使传统车身生产模式发生变革。
受益于新一代压铸工艺,大型压铸机市场需求有望启动。若只考虑车身底板使用,我们在以下三种情形下测算市场空间:1)若特斯拉产能100%使用,预计2020-2030年大型压铸机平均空间为10.8亿元/年;2)若所有新能源乘用车产能均使用,预计2020-2030年平均空间有望超40亿元/年;3)若远期来看,假设所有汽车产能均使用,则远期市场空间达137亿元/年。特别的,长远期来看,若假设其他车身结构件也能应用一体化压铸,且设备更换周期为10年,则我们估算,远期大型压铸机市场空间有望达480亿元/年。
设备是实现一体化压铸的核心难点,具有较高壁垒。一体化压铸工艺涉及复杂、大型、高精密零件的一体成型,对于压铸机的锁模力、压射量和控制能力存在硬性要求。我们认为,大吨位压铸机由于其高难度与创新性,在技术、供应链、工艺控制等方面具有较高壁垒,先进入者容易建立较强的竞争优势。
风险
新工艺渗透不及预期;压铸机研发不及预期;压铸机产能不足。
正文
压铸机:金属热加工成型设备,广泛应用于汽车制造
压铸机:应用广泛的金属热加工成型设备
压铸工艺是利用模具腔对融化的金属施加高压。压铸是铸造工艺中应用最广、发展速度最快的金属热加工成型工艺方法之一,其原理是利用压铸机把熔融金属液压射到模具中冷却成型,开模后得到固体金属铸件,模具通常是由强度更高的合金加工而成的。压铸机根据锁模力的大小可分为小型(160-400吨),中型(400-1,000吨)和大型(大于1,000吨)压铸机,通常大型压铸机还会配备机械手等周边设备,形成压铸单元岛。
镁、铝合金为主要压铸材料。压铸件合金材料以有色金属及其合金为主,其中铝合金用量最大,根据《中国铸造年鉴(2016年版)》,铝合金压铸件在压铸件中占比约为85%。此外,镁合金压铸件的应用也逐步扩大,尤其在汽车压铸件的应用领域;而锌合金压铸件的产量逐步减小,多属于中小零件,铜合金压铸件产量较少,黑色金属及其合金压铸件则长期都处于停顿状态。
图表:压铸机示意图
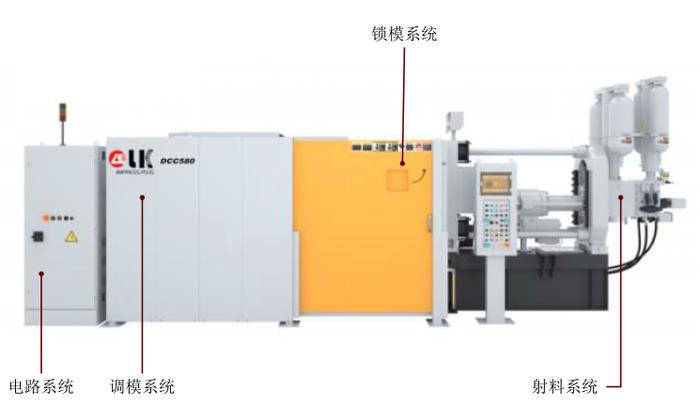
资料来源:力劲集团官网,中金公司研究部
图表:压铸机工作原理
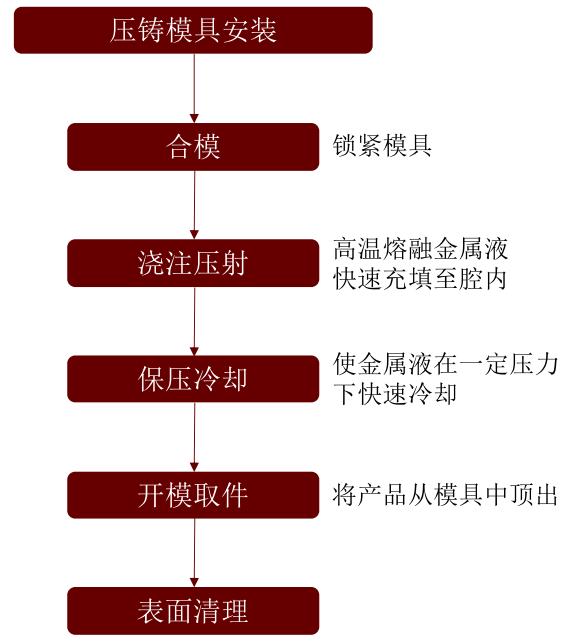
资料来源:中国汽车材料网,中金公司研究部
压铸机的下游应用以汽车为主。压铸件目前广泛应用于汽车、机械、家电、通讯和五金等领域,其中以汽车行业用量最大。按下游来看,根据广东省机械工程学会压铸分会2012年《中国压铸机械行业现状及发展趋势》报告,估计汽车和摩托车占比65%,家电、3C、机电工具和建材等占比分别为9%、9%、9%和8%。而根据中国铸造协会《中国铸造年鉴(2016年版)》,2016年中国压铸产品中用于汽车行业的比例已达75%,汽车行业对压铸件的重要性不断提升。
图表:压铸机应用领域分布(2012年):汽车应用占主导
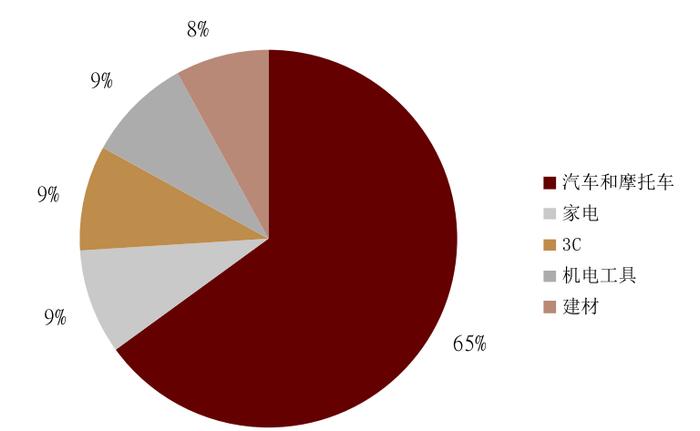
资料来源:广东省机械工程学会压铸分会,伊之密招股书,中金公司研究部
车用压铸件应用广泛,向集成化结构件发展
压铸件已在汽车行业得到大范围应用。在环保和节能的要求下,汽车制造不断走向轻量化,推动了密度低、比强度高的铝、镁合金等在汽车零部件上的广泛应用。车用铝合金的制造工艺主要有冲压、压铸和挤压成型,压铸则是铝合金部件的主要生产方式,根据咨询公司DuckerFrontier在2020年7月对北美车用铝合金的调查报告,预计2020年压铸件用量占车用铝件的65%。
在结构件应用的空间较大,有望快速增长。对于铝合金铸件而言,按照单车用铝量计算,压铸件在发动机(缸体、缸盖、进气管等)、变速器壳体、轮毂等非结构件中应用较为广泛。而在结构件中,压铸件也应用在底盘悬架、白车身结构件(横纵梁、减震塔等)、覆盖件、内饰件等部件上。目前压铸工艺在结构件的渗透率仍较低,例如根据DuckerFrontier,2020年压铸件在减震塔的渗透率仅约10%,但有望不断受益于轻量化趋势与加工工艺成熟,实现快速增长,预计用于结构件的压铸件用量2016-2020年CAGR、2020-2022年CAGR分别达到20%和8%。
图表:北美车用铝合金分部件用量占比(2020E)

资料来源:DuckerFrontier(2020.7),中金公司研究部
图表:汽车用铝合金压铸件应用举例
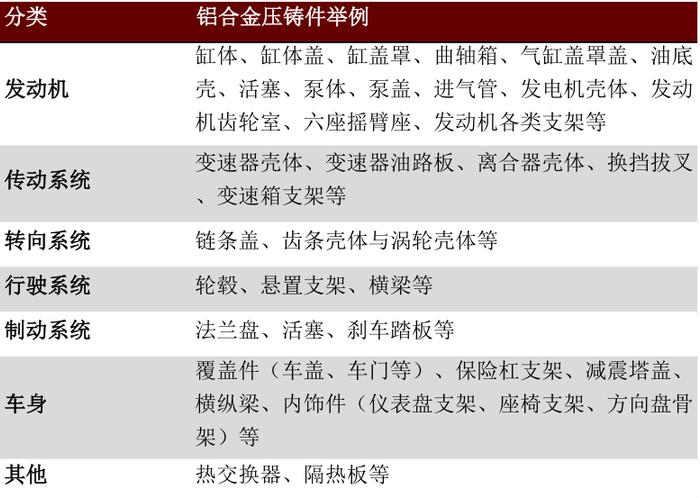
资料来源:《压铸铝合金研究现状与未来发展趋势》(樊振中等,2020),中金公司研究部
图表:北美车用铝合金分工艺用量情况
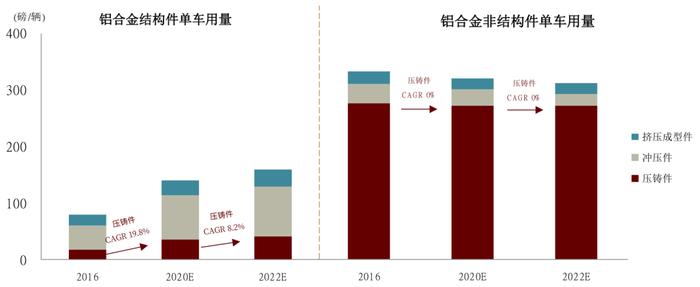
资料来源:DuckerFrontier(2020.7),中金公司研究部 注:根据DuckerFrontier的定义,结构件包括白车身(覆盖件、车身结构件、加强件)、底盘结构件(悬架、支架、副车架)以及新能源汽车的电池箱体
受益于压铸机吨位和新能源汽车的发展,压铸件向大型化、集成化发展。随着压铸机的锁模力不断提升,以及压铸材料和压铸工艺的不断完善,汽车压铸件向大型化与集成化发展。车门框、A柱、后纵架、尾箱盖等大型车身结构件可通过压铸生产、组装而成,同时所需求的压铸机吨位也提升至4,000吨以上。此外,压铸件集成化有助于减少零件重量和工序数量,例如奥迪部分车型减震塔铸件以1个零件替换原本由10个零件焊接而成的钢制减震塔,可实现减重10.8千克。目前集成化的压铸结构件在部分豪华车车型中已得到较多应用,如奥迪(A8、Q8等)、奔驰C系、宝马X系等。
图表:压铸件在大型车身结构件上的可行应用
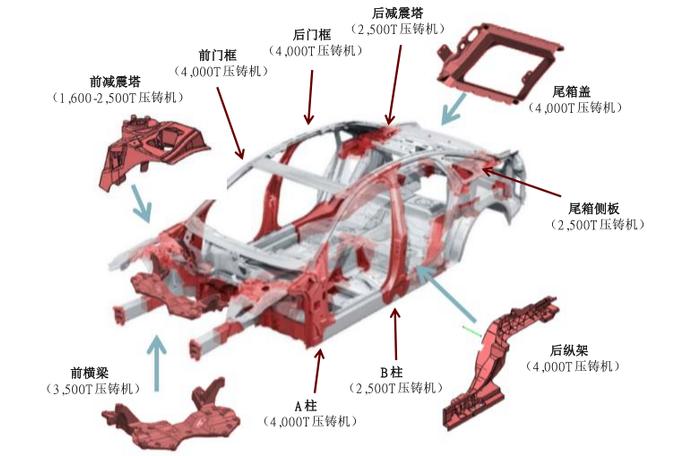
资料来源:布勒公司,《中国汽车结构件压铸现状》(卢宏远,2017),中金公司研究部
图表:奥迪Q8全铝车身及结构化减震塔部件示意图
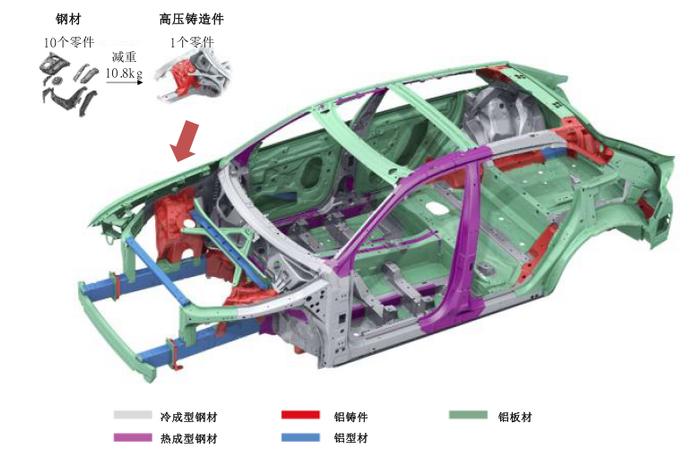
资料来源:公司官网,《Correlation between process parameters and quality characteristics in aluminum high pressure die casting》(Winkler M, et. al,2015),中金公司研究部
新能源汽车中铝件用量将增加,其中我们认为压铸件的占比有望提升。新能源汽车受动力电池重量、动力电池续航里程的限制,对于轻量化的需求更为迫切,因此在车身结构件等大型零部件中更多地应用铝合金。根据DuckerFrontier,纯电动车相比于燃油车,单车铝合金用量增长约42%,增加的部分主要是动力传动系统,如牵引电机外壳、齿轮箱和其他铝制壳体,以及车身结构件、覆盖件等。虽然DuckerFrontier认为车身结构件和覆盖件等铝制品有相当一部分是冲压或者挤压工艺成型,但我们认为,随着一体化压铸工艺的成熟,压铸工艺有望替代冲压等其他工艺,未来铝合金压铸件在新能源汽车中的用量有望快速提升。
图表:北美燃油车与电动车单车用铝量对比
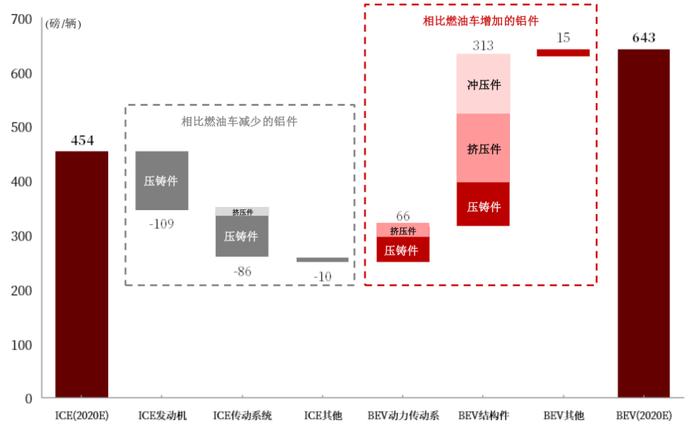
资料来源:DuckerFrontier(2020.7),中金公司研究部 注:ICE为内燃机汽车,BEV为纯电动车
一体化压铸:变革式制造工艺,效率成本大大优化
常规汽车结构件制造工艺:包含冲压成型和焊接两道核心工序
传统汽车车身的制造需要对数百种结构件进行数千次焊接。传统汽车的骨架制造是先用模具,将钢或铝合金通过冲压、挤压、铸造等工艺加工成结构件,再通过焊接、铆接等方式连接。通常而言,一辆轿车的白车身、底盘分别约占总车重的35%、34%,白车身一般由300-400个零件组成,焊点数量可达4,000-6,000个,底盘结构件则主要包括前后副车架、控制臂、转向节、悬架连杆等多种复杂结构件。因此汽车骨架的制造工序繁多,生产时间也较长。设备方面,零部件的成型一般通过标准化的冲压机床、挤压成型机或压铸机制造,焊接则普遍应用机器人进行自动化生产,因此设备投资额较高。
图表:汽车车身组装示意图
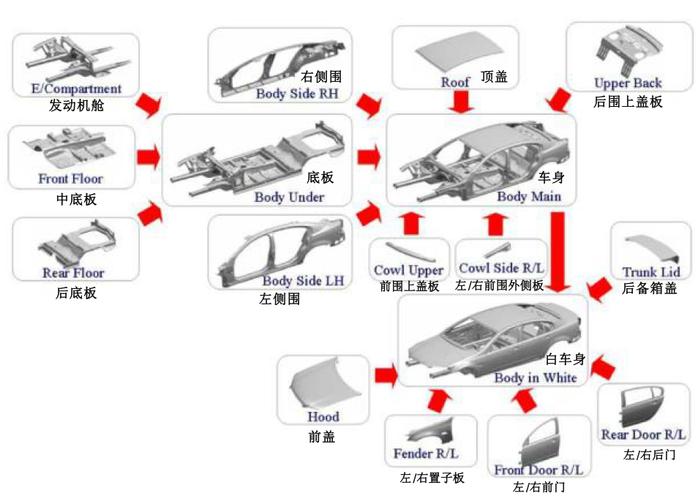
资料来源:Hokuto公司官网,中金公司研究部
一体化压铸:颠覆传统工艺,一次压铸成型
一体化压铸工艺包括一体化设计和一次成型。一体化压铸工艺是将原本设计中需要组装的多个独立的零件经重新设计,使用压铸机进行一次成型,从而直接获得完整的零部件,实现原有功能。由于压铸工艺比冲压、挤压等工艺更适合于生产形状复杂的大型零件,因此一体化压铸有望成为汽车结构件走向大型化、集成化的必备选择。
特斯拉引入一体化压铸工艺,有望引发车身生产模式大变革。特斯拉2020年首次将一体化压铸技术应用于Model Y的车身后底板制造。我们认为,特斯拉大规模地应用一体化压铸工艺,有望带来“鲶鱼效应”,引发其他新能源车厂乃至传统车厂效仿,或许将使得传统车身生产模式发生变革。
工艺优点:零件数量大大减少,带来多方面的效率成本优化
从实现效果看,我们认为一体化压铸工艺与传统“成型+焊接”的车身制造工艺相比,具有以下明显优点:
► 轻量化:在大尺寸结构件上充分利用铝合金的低密度特性,有望大幅度减轻车身重量。根据特斯拉在其2020年电池日的表述,通过车身制造方式和电池工程的改变,可以将车重降低10%。
► 提效降本:通过一次压铸成型,大大减少零部件的生产线数量,并减少焊接环节的工序,从而缩短生产周期。我们估计,今年6,000吨大型压铸机生产一个部件的单位时间有望达到90-120秒;而若以“成型+焊接”的方式生产,同样生产车身底板后部,对70多个结构件进行冲压然后焊接则需要耗费更大的时间成本。除此之外,一体化压铸可实现以一台压铸机代替多条成型和组装生产线,从而大大减少人员、设备及土地等制造成本。
► 提高零件强度:一体化压铸避免了焊接造成的强度降低,同时在设计零件时可不考虑安装孔、安装位置等要素,从而使用更优化的工程学结构。此外,需要说明的是,铝合金材料可能成为其中一个瓶颈,主要在于部分新能源车部件(如转子、逆变器)同时要求材料具有高强度和高电导率,而常规的铝合金材料难以同时满足,例如常用的A356屈服强度大于175Mpa,但电导率仅40%,反之莱茵Castasil-21电导率最高达48.5%,但强度仅85-100Mpa,特斯拉通过调整合金配比,研发出强度90-150Mpa、电导率40%-60%的铝合金材料[1],有望部分解决这一瓶颈问题。
应用现状:已用于Model Y的后底板制造,零件“七十化一”
Model Y后底板通过使用6,000T压铸机一体成型,将70个零件简化为1-2个。根据特斯拉公司公告,其在美国、上海以及正在建设的柏林工厂均部署了多台6,000T吨位的大型压铸机,用于Model Y后底板的一体化压铸。相比于Model 3后底板的70个零件,Model Y采用一体化压铸工艺后,零件数减少为1-2个。根据马斯克在特斯拉电池日的表述,这一制造过程可降低40%的后底板制造成本。
图表:Model Y后底板应用一体化压铸工艺
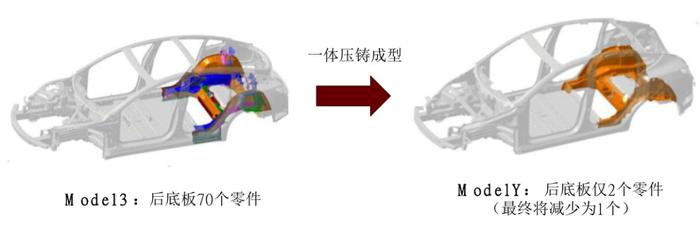
资料来源:特斯拉公司公告,中金公司研究部
图表:特斯拉上海超级工厂Model Y压铸车间
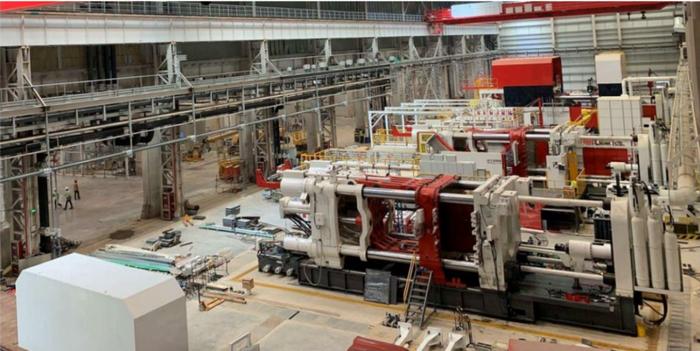
资料来源:特斯拉公司公告,中金公司研究部
未来发展:从Model Y到Cybertruck,从后底板到其他结构件
Cybertruck应用有望跟进,压铸机吨位继续升级。根据马斯克在特斯拉4Q20业绩电话会议上的表述,特斯拉将在新一代皮卡Cybertruck的后底板继续应用一体化压铸技术,并且由于Cybertruck车身更长,将应用更大吨位的8,000T压铸机进行铸造。我们认为,一体化压铸工艺有望在特斯拉新车型、新产线中普遍应用,而对于已量产车型与已有产线,虽然由于原有产线完备、转换成本较高,该技术暂未应用,但我们认为在后续的产线升级换代中,一体化压铸技术也有希望引入。
未来有可能在底板前部、中部以及车身结构件上进行应用。目前特斯拉主要将该技术应用于底板后部的一体成型,而在底板前部、中部以及车身结构件(侧围、顶盖、后盖板等)的应用空间仍非常广阔。我们认为,一体化压铸从底板后部向其他部位的应用拓展具有技术可迁移性,例如铝合金材料、模具设计原理均是互通的。因此我们认为,汽车底板后部一体化压铸的成功实施,有望促进未来在底板前部、中部以及车身结构件上的应用。
图表:特斯拉Cybertruck示意图
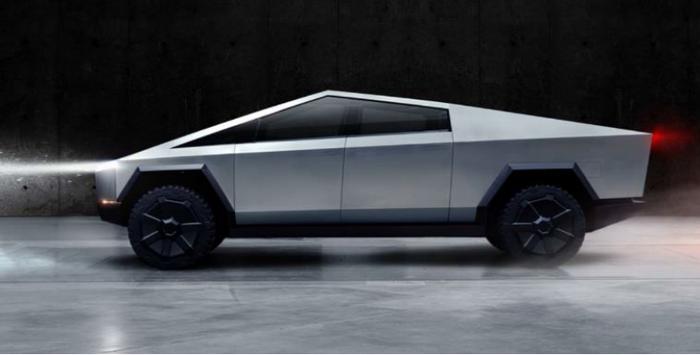
资料来源:特斯拉官网,中金公司研究部
最终愿景:彻底颠覆传统,实现一次压铸成型
多面一体压铸机专利面世,目标是“像制造玩具车”一样造车。2019年7月特斯拉发布名为“汽车车架的多面一体成型铸造机和相关铸造方法”的专利,根据专利信息,该压铸机包括一个具有车身覆盖件模具的中心部分,以及多个可相对覆盖件模具平移的凸压模具部分,多个凸压模具可在中心区汇合后,负责不同部件的压铸,最终完成完整或部分的一体式车架铸造。虽然目前该专利方案并未得到商业化,但我们认为其构想是颠覆性的,若能完成整体车身由单一压铸机一体成型,则有望完全取消原有的组装生产线,并很大程度地降低车身制造成本(包括但不限于工厂运营成本、工具成本、时间成本、人工及其他设备成本)。
图表:特斯拉一体成型压铸机专利示意图

资料来源:Patentscope,中金公司研究部 注:标黄为各个压铸单元
设备为核心难点,力劲科技率先突破
大吨位压铸机设备是实现一体化压铸的关键。一体化压铸包括一体化设计和一次成型两个维度,其中一体化设计表现在模具的设计,包括模具结构、型芯、冷铁的配置等,主要依赖大量设计经验以及计算和实验;而由压铸机及配套设备组成的压铸单元则属于一次性成型的必备设备。为了满足大尺寸零件的制造要求,并保证其强度和量产效率,压铸机的锁模力、模板尺寸、压射量都需要同步提升,同时一体化成型势必涉及高精密零件,对压铸机的压射压力及速度的控制也带来较高的要求,具有较高的技术难度。同时,压铸机还需要在快速的大规模生产过程中保持高良率,实现生产部件的一致性和稳定性,这需要压铸机生产厂商在工艺know how端有较为深度的积累。
力劲科技及子公司意德拉率先量产大吨位压铸机并供货特斯拉。力劲集团成功突破6,000吨合模力的大型压铸单元,并与意大利子公司意德拉共同为特斯拉的全球工厂供货。根据意德拉官网产品介绍,6,200吨大型压铸机设备长19.5米,自重430吨,相比于其他大型压铸机产品,在合模力、压射力、模板尺寸、射料量上均有明显突破。
2021年力劲发布9000吨大型压铸机,将压铸机的吨位再向前推进一步。2021年4月21日,力劲科技面向全球首发了世界最大的DREAMPRESS9000T巨型智能压铸单元,再次引领了全球大型压铸装备制造技术的发展。该设备未来有望应用于更大规格零部件的一体化生产。该设备目前已经获得瑞立集团的订单。
图表:意德拉不同吨位压铸机产品的性能对比
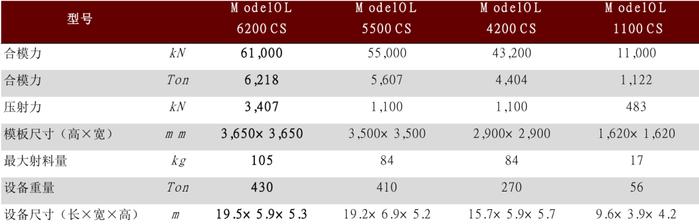
资料来源:意德拉公司官网,中金公司研究部注:仅列举其中四款产品
大吨位压铸机壁垒高筑,短期内不易被逾越。我们认为,力劲集团作为压铸机行业的龙头与大吨位压铸机的先行者,具有明显的先发优势和竞争壁垒,我们认为主要体现在:
► 技术优势。公司技术团队成熟完备,专注于前沿科技研究,并与清华、浙大、北化等高校进行科研合作,技术创新能力强。例如公司自主研发出高性能射料系统,最大空压射速度可超过10m/s,最短建压时间小于30ms,压射加速度超过50g,适合大型薄壁结构件生产工艺需求等。
► 供应链优势。公司为行业内少有的具备垂直制造能力的公司,公司在辽宁阜新拥有占地面积超过15万平方米的钢铁铸造基地,以保障原材料的稳定供应和技术的灵活创新。例如在大型压铸机中,需要实现大型沉重板件的反复移动,因此对压铸机零件的尺寸精度、定位精度和力学性能构成了较大考验,常规生产设备无法满足,得益于垂直化优势,公司自主改进了铸造模具、车床、磨床、热处理设备等,从而实现大型零件的生产及组装。
► 客户优势。公司与特斯拉建立了合作研发与稳定供货的伙伴关系,我们认为这有望成为公司进入其他车企供应体系的“敲门砖”。
► 工艺经验优势。我们认为,公司在大型压铸机领域具备先发优势,且率先积累了一体化压铸机的工艺经验,在良率控制和参数设计等方面均领先于竞争对手,同时已经率先布局更大吨位的9,000T压铸机,公司有望在未来产品竞争中,掌握质量与良率的领先优势。
新一代压铸工艺有望带动大型压铸机需求快速增长
我们认为,大型压铸机作为新一代压铸工艺的首要设备,需求有望迎来快速增长。目前新一代压铸工艺为特斯拉率先使用,考虑其在汽车轻量化、降成本上的领先作用,我们认为未来一体化压铸在其他品牌的新能源车,甚至传统车上也有望应用,长期成长性强。因此,我们在以下三种假设情形下,分别测算大型压铸机的市场空间:1)假设一体化压铸工艺仅被特斯拉应用;2)假设一体化压铸工艺在各品牌新能源乘用车均得到应用;3)假设一体化压铸工艺在新能源乘用车和传统乘用车均得到应用。
考虑到大吨位压铸机的产业化进展以及特斯拉的示范性作用,我们认为,一体化压铸工艺有较大可能率先在车身底板大范围应用,因此我们首先测算在车身底板上应用的市场空间;进一步地,我们将测算在其他车身结构件也采用一体化压铸的情形下,大型压铸机的市场空间。
核心假设:1)产能:我们假设生产一个结构件的时间为2-3分钟,一台压铸机的年产能为10万件/年;2)台数:目前一体化压铸后底板需要1台6,000吨压铸机,我们假设完成全部车身底板需要3台6,000吨压铸机(前、中、后);3)价格:目前大型压铸机较为定制化,未形成统一定价,我们粗略假设6,000吨压铸机单价为4,000万元。
若仅应用于车身底板:长期大型压铸机年化市场空间天花板有望超百亿元
情形一:仅为特斯拉使用,预计大型压铸机市场空间为10亿元左右量级
► 中短期:假设特斯拉新增产能100%使用,预计2021、2022年市场空间为6.5、6.6亿元。考虑到中短期内,原有产能转化工艺的成本较高,我们假设一体化压铸工艺仅在新增产能中使用。我们测算若在特斯拉新增产能中100%使用,2021、2022年大型压铸机需求量约为16、17台,对应市场空间(天花板)约为6.5、6.6亿元。中金汽车组预计,到2025年特斯拉产能达355万辆,相对应2025年大型压铸机市场空间约为9.0亿元。
图表:大型压铸机市场空间测算(情形一)
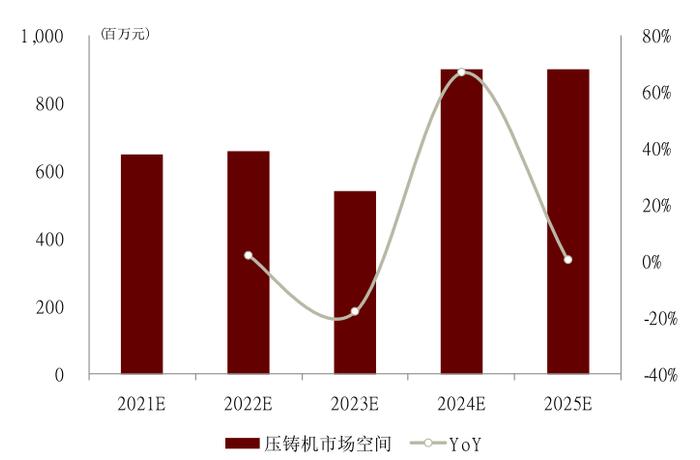
资料来源:公司公告,中金公司研究部汽车组
► 中长期:假设到2030年特斯拉全部产能100%使用,则预计2020-2030年年均市场空间为10.8亿元。假设到2030年,车身底板的一体化压铸工艺在特斯拉全部产能中都应用。若100%应用一体化压铸,我们估计大型压铸机在2030年保有量为189台,对应2020-2030年均市场空间为7.6亿元,若假设中长期产能利用率为70%,则最终市场空间可达10.8亿元。
图表:大型压铸机2020-2030年均市场空间测算及敏感性测试(情形一)
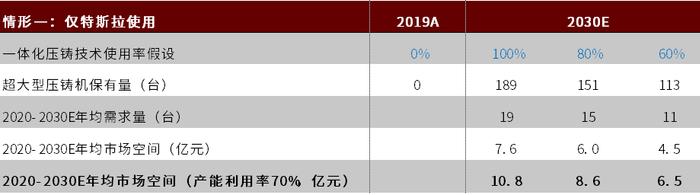
资料来源:公司公告,中金公司研究部汽车组
情形二:在各品牌新能源乘用车均使用,预计大型压铸机市场空间为~40亿元量级
► 中短期:假设新能源乘用车新增产能100%使用,则2025年市场空间有望达到40亿元以上。若假设一体化压铸工艺仅在新能源乘用车新增产能中使用,根据中金汽车组预计,2021、2022年全球新能源乘用车销量分别为374、538万辆,同比增长58.8%、43.7%,新增销量达138、164万辆。假设产销平衡,我们预计2021、2022年大型压铸机需求量约为42、49台,对应市场空间约为16.6、19.6亿元。假设到2025年,全球新能源乘用车销量达1,240万辆,对应2025年大型压铸机市场空间约为29.4亿元。此外,考虑到新能源车产能规划可能超出实际销量,该测算存在低估的风险,假设产能利用率为70%,则到2025年市场空间有望达到42.0亿元。
图表:全球新能源乘用车销量预测
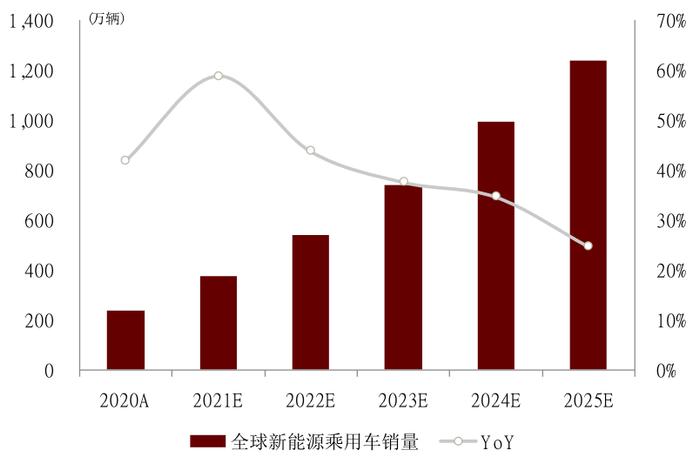
资料来源:中汽协,Marklines,中金公司研究部汽车组
图表:大型压铸机市场空间测算(情形二)
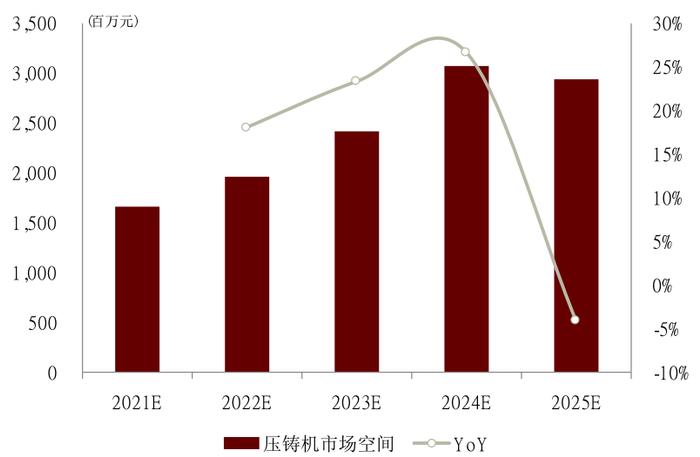
资料来源:中汽协,Marklines,中金公司研究部汽车组
► 长期:假设2030年新能源乘用车全部产能100%使用,预计2020-2030年年均市场空间为43.1亿元。若假设到2030年,车身底板的一体化压铸工艺在新能源汽车全部产能中使用,根据中金汽车组,预计2030年全球新能源乘用车销量达2,514万辆,据此我们估计大型压铸机在2030年保有量为754台,对应2020-2030年年均市场空间为30.2亿元,若假设产能利用率为70%,则2020~2030年年均市场空间有望达到43.1亿元。
图表:大型压铸机2020-2030年均市场空间测算及敏感性测试(情形二)
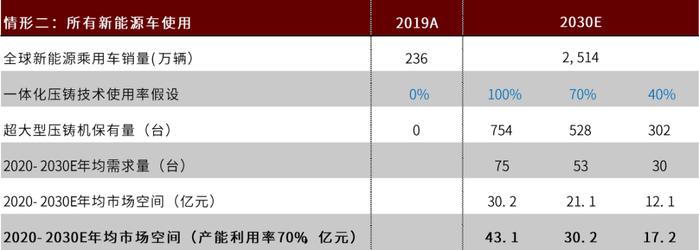
资料来源:中汽协,Marklines,中金公司研究部汽车组
情形三:在新能源车与传统车均使用,预计远期大型压铸机市场空间可达137亿元
考虑到传统车也存在轻量化的需求,假设远期一体化压铸工艺在乘用车全部产能中使用。根据中金汽车组,2020年全球乘用车销量达5,979万辆,若预计未来年均复合增长率约2%,则2050年全球乘用车销量约为8,000万辆,据此我们估计大型压铸机远期保有量为2,400台,假设压铸机更新替换周期为10年,且假设远期产能利用率为70%,则大型压铸机仅在汽车底板应用的远期稳态市场空间有望达到137.1亿元。
图表:大型压铸机远期市场空间测算(情形三)
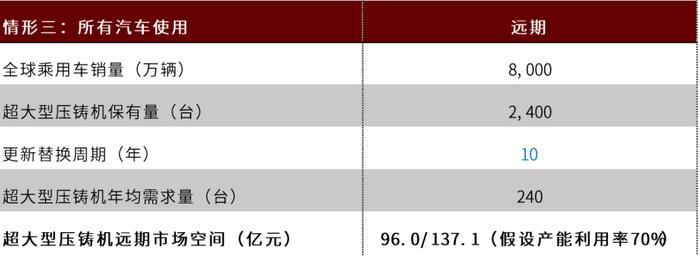
资料来源:乘联会,Marklines,中金公司研究部汽车组
若主要车身结构件均用一体压铸:大型压铸机最终年均市场空间或可达480亿元
假设最终,汽车主要车身结构件均可应用一体压铸成形工艺。目前大型压铸机主要应用于车身底板,但随着技术的进步,我们假设未来其他车身结构件也逐步采用一体化压铸的方式,我们根据车身各部位的大小及复杂程度,假设汽车车身底板可通过3台6,000T压铸机一体压铸成形,顶盖/尾盖各使用1台6,000T压铸机,左右侧围各使用1台8,000T压铸机,车门共使用4台4,000T压铸机,则我们估算大型压铸机最终保有量约8,800台,若替换周期10年,假设远期的产能利用率为70%,则市场空间有望达到480亿元。由于目前除后底板外,其他车身部位的一体压铸工艺均未经实践验证,未来应用具有一定不确定性,因此以上测算仅供投资者参考。
图表:若全车身一体压铸成形,大型压铸机市场空间测算(仅供参考)
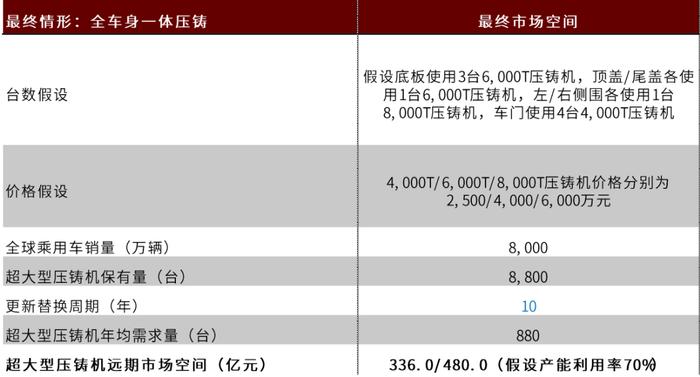
资料来源:乘联会,Marklines,中金公司研究部汽车组
图表:各情形市场空间测算汇总表

资料来源:公司公告,中汽协,乘联会,Marklines,中金公司研究部汽车组
大型压铸机的领先者和潜在参与者梳理
力劲科技:压铸机行业龙头,率先突破大吨位产品
全球压铸机行业龙头,拥有力劲和意德拉两大压铸机品牌。力劲科技集团有限公司由刘向尚先生于1979年在香港创立,1980年推出第一代热室压铸机。2006年,力劲科技在香港交易所上市。2008年,公司收购了当时的意大利知名压铸机公司意德拉。公司在全球压铸机行业保持多年的领先地位,截至目前,公司在全球已拥有8个主要生产基地,分布于全国5个省份以及中国台湾和意大利(意德拉)。
图表:力劲科技历史沿革
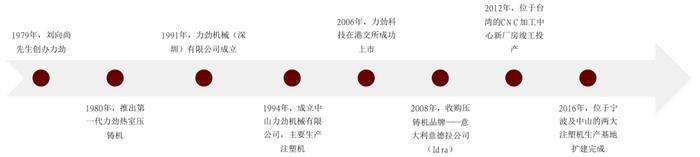
资料来源:公司官网,中金公司研究部
公司股权结构较为集中,目前为二代执掌经营管理。公司创始人刘向尚及其配偶张俏英为实际控制人,二人直接或通过Girgio Industries Limited间接持股65.37%,股权结构较为集中。刘向尚的儿子刘卓铭任公司行政总裁及执行董事。
图表:力劲科技股权结构(截至2021年3月31日)
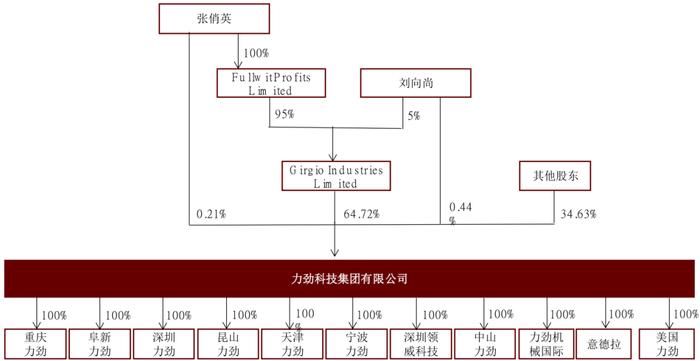
资料来源:公司公告,中金公司研究部
压铸机品类齐全,大型压铸机不断突破。公司产品包括压铸机、注塑机和数控加工中心,其中压铸机收入占2020财年收入的69%。公司压铸机品牌包括力劲和意德拉,力劲品牌拳头产品为IMPRESS冷室压铸机,合模力区间覆盖130t-6,000t,意德拉品牌压铸机产品包括OL CS系列(合模力从420t-6,200t)、OL R系列、XPRESS系列以及NOX系列。公司6,000t以上大型压铸机产品助力特斯拉实现一体化压铸技术,独供特斯拉的中国及海外工厂。进一步地,2021年4月21日公司9,000t大型压铸单元“Dreampress”实现向汽车零部件龙头企业瑞立集团发货,发货现场同时签订了6,800t、8,000t智能压铸单元订单,我们认为这体现了公司大型压铸机在吨位不断突破的同时,客户认可度高,未来更多订单的落地可期。
图表:力劲科技产品矩阵
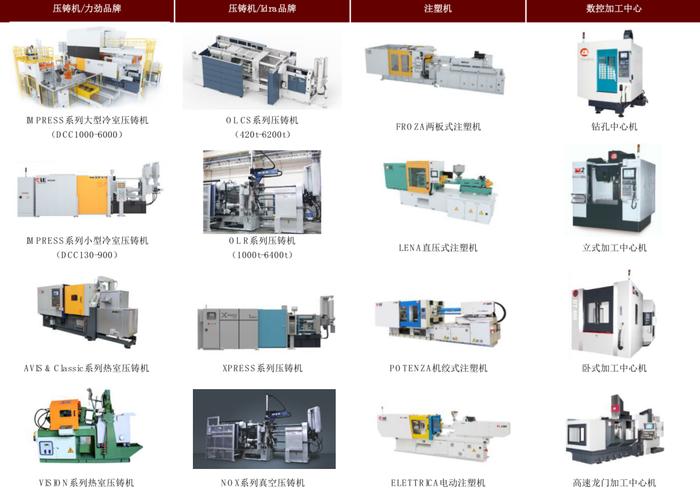
资料来源:公司官网,中金公司研究部
图表:力劲科技分产品营收占比(FY2020)
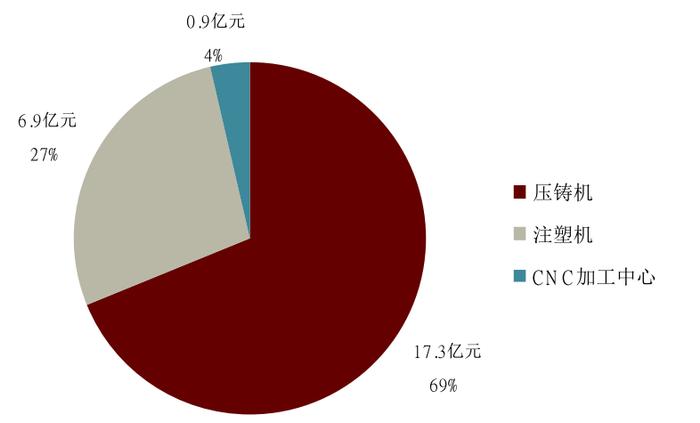
资料来源:万得资讯,公司公告,中金公司研究部 注:2020财年为2019.4.1-2020.3.31
压铸机收入稳步上升,整体毛利率维持在25%左右。2014财年至2019财年,公司压铸机收入从14.2亿元提升至21.9亿元,年均复合增速9%。2020财年公司实现压铸机收入17.3亿元,同比下降21.1%,主要受下游汽车行业景气度下降,资本开支意愿低迷的影响。公司整体毛利率较为稳定,保持在25%左右。
图表:力劲科技压铸机业务收入及增速情况

资料来源:万得资讯,公司公告,中金公司研究部
图表:力劲科技综合毛利率情况
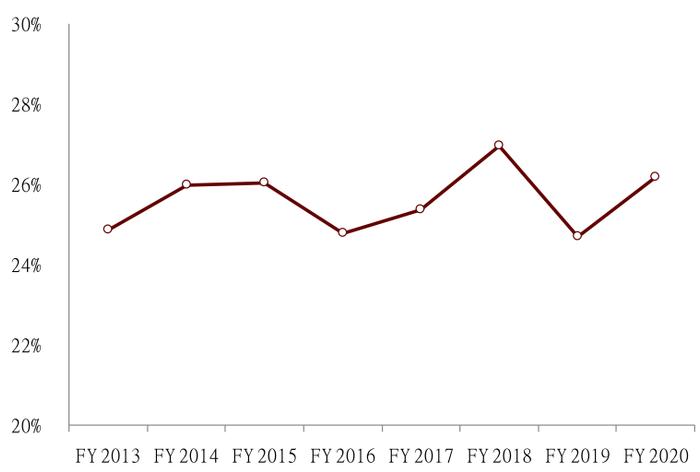
资料来源:万得资讯,公司公告,中金公司研究部 注:公司未披露分产品毛利率,此处为整体毛利率
大型压铸机的潜在参与者:关注伊之密、海天集团
伊之密:全国领先的模压成型装备制造商
伊之密是全国领先的模压成型装备制造商。广东伊之密精密机械股份有限公司创立于2002年,具有注塑机、压铸机、橡胶注射成型机、高速包装系统、机器人自动化集成系统和精密模具等6个事业部,致力于为客户提供整套生产解决方案。2004年公司成立压铸机事业部,2019年聘用欧洲压铸行业专家史蒂芬·费睿泽担任压铸机金属成型首席战略官。
伊之密的压铸机技术品质领先,具有控制精度高、节能效果好等特点。公司不断加强研发投入,开发了压铸机高效及自动化生产技术、智能化在线品质监控技术、压铸机实时控制技术、压铸机自动控制技术等一系列核心技术,应用于DM重型冷室机、DM高效节能冷室机和DM-ARC实时控制冷室机等产品系列。2020年公司压铸机收入占比16%。
新产品不断推出。公司2014年完成H系列高性能镁铝合金压铸机的开发工作,2015年将该产品重点推出市场,并在2016年全面推广。目前公司压铸机最大机型合模力达4,500吨,我们认为公司具有向更大机型产品突破的潜力。
图表:伊之密压铸机产品
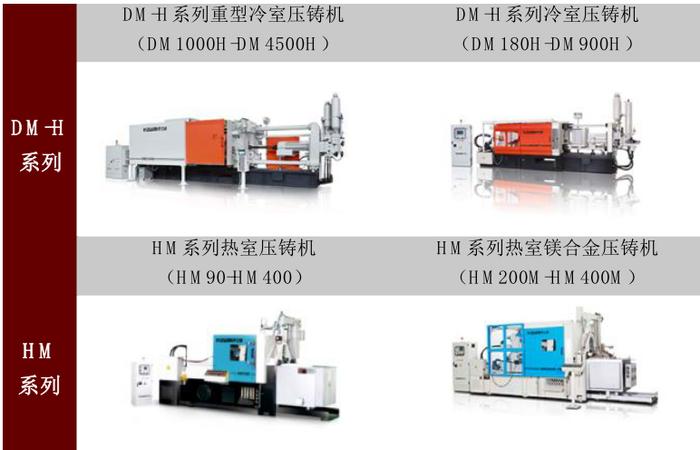
资料来源:公司官网,中金公司研究部
图表:伊之密分产品营收占比(2020年)
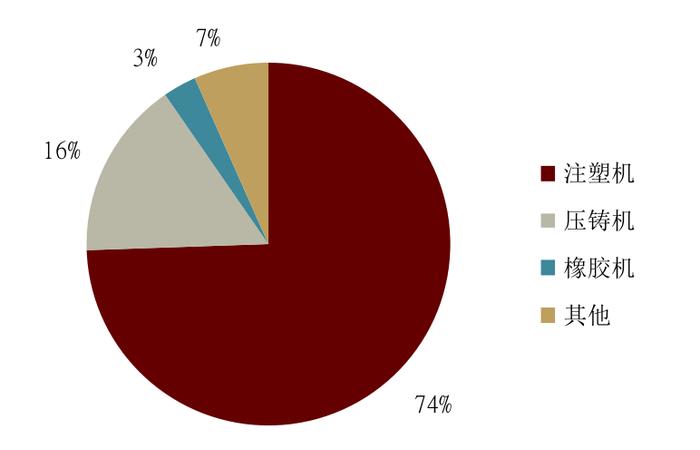
资料来源:公司公告,中金公司研究部
收入水平保持稳定,盈利能力突出。公司压铸机市场份额行业第二,仅次于力劲科技。公司压铸机的盈利能力突出,除2020年受疫情影响外,毛利率始终维持在34%以上,高于力劲科技的水平。公司压铸机毛利率从2011年的34%提升至2016年的42%,2017年以来有所下滑,主要是受行业竞争加剧、下游汽车行业需求低迷以及疫情的影响。
图表:伊之密压铸机业务收入及增速情况
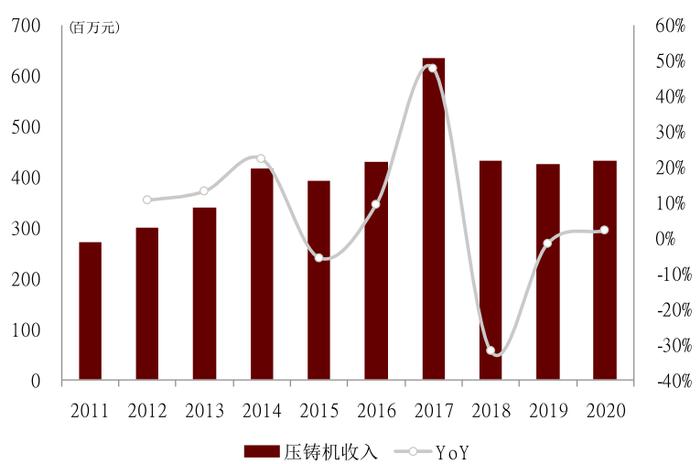
资料来源:公司公告,中金公司研究部
图表:伊之密压铸机业务毛利率情况
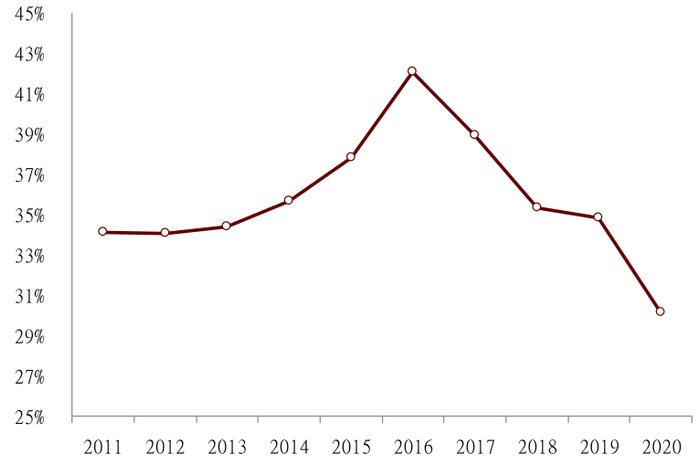
资料来源:公司公告,中金公司研究部
海天集团:2016年进入压铸机行业,近年发展迅速
海天集团2016年成立子公司海天金属,此后快速发展。宁波海天金属为海天集团全资子公司,2016年成立并开始研发第一代压铸机,公司2017年4月至2018年9月间在全国设立了18个经销网点,服务面积已覆盖50%省份。2018年由海天集团投资1.6亿元在宁波保税区建立压铸机新基地,彰显集团发展该业务的信心。
公司拥有HDC和HDM两大系列产品。公司产品包括HDC系列冷室压铸机和HDM系列冷室压铸机(采用德国进口压射系统)。公司引进日本三菱重工、德国SHW、德国瓦德西里、捷克斯柯达等大型进口加工中心,坚持产品的重要零部件100%自主加工,并可在产品中选配全实时控制压射系统、云系统等。2019年,公司4,500吨压铸机及压铸岛成功交付并使用,显示公司的产品竞争力逐步提升。
图表:海天金属发展历程
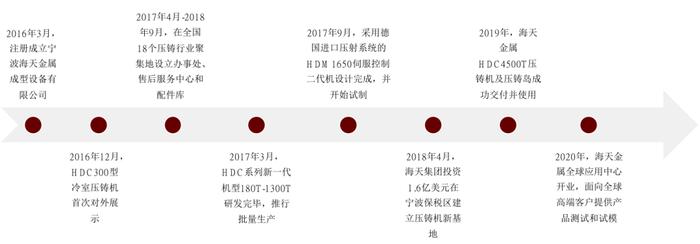
资料来源:公司官网,中金公司研究部
瑞士布勒:历史悠久的欧洲压铸机厂商
布勒集团为欧洲著名的加工设备及解决方案提供商,拥有超过160年的历史。布勒集团旗下拥有谷物食品(制粉、仓储设备)、消费食品(烘焙、饼干、糖果加工设备)、先进材料(压铸机、研磨与分散设备、镀膜设备)三大事业部。根据公司年报,布勒集团2019年总营收270亿瑞士法郎(约合193亿人民币),其中先进材料事业部营收4.4亿瑞士法郎(约合31亿人民币)。
压铸机产品覆盖四个系列,锁模力范围达340-5,600吨。布勒集团拥有瑞士、美国和中国江苏三大压铸机生产基地,以及Carat、Fusion、Evolution、Ecoline S四个系列压铸机产品,同时公司可为压铸机配套SmartCMS压铸岛智能管理系统、打码机、真空系统等设备。2019年10月公司Carat 560(锁模力5,600吨)压铸机产品供应韩国瑞进(Seojin System),用于生产5G基础设施部件和电动汽车电池外壳,该型号产品也在2020年11月于中国市场发布。此外,Carat 610(锁模力6,100吨)的压铸机产品也在同步研发中,有望于近期推向市场。
图表:布勒集团压铸机产品
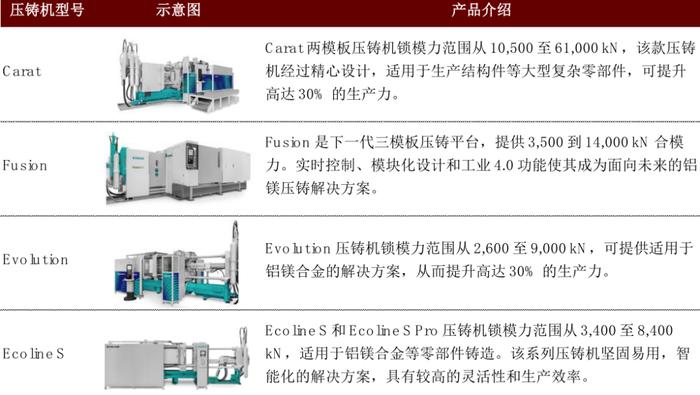
资料来源:公司官网,中金公司研究部
风险
1)新工艺渗透不及预期。新的一体化压铸工艺尚处于应用的初期,目前仅用于特斯拉的Model Y后底板制造,如果新工艺由于种种原因(如技术、资金等),在其他车身结构或汽车车型中难以推广,则可能造成大吨位压铸机需求不及预期。
2)压铸机研发不及预期。一体化压铸未来应用的拓展,仍依赖压铸机吨位的进一步提升,考虑到大吨位压铸机具有较高的技术难度,若压铸机的性能提升遭遇瓶颈,可能造成新工艺无法顺利推进。
3)压铸机产能不足。目前行业内能够提供大吨位压铸机的公司较为稀缺,短期内其他公司能否突破存在一定不确定性,因此存在大吨位压铸机产能不足的风险。
-----
[1] 详见特斯拉专利2020年2月发布的专利
《Aluminum alloys for die casting》https://patentscope2.wipo.int/search/en/detail.jsf?docId=WO2020028730&tab=PCTBIBLIO
文章来源
本文摘自:2021年5月21日已经发布的《“一体压铸”:车身制造之变革》
分析员 张梓丁SAC 执业证书编号:S0080517090002
分析员 邓 学 SAC 执业证书编号:S0080521010008
分析员 陈显帆 SAC 执业证书编号:S0080521050004